联系电话
- 联系人:
- 钱峰
- 电话:
- 86-0512-65350149
- 手机:
- 18914081572
- 售后:
- 13812694460
- 传真:
- 86-0512-65867868
- 地址:
- 苏州市相城区黄桥永方路168号
- 个性化:
- www.zh-wedm.com
- 网址:
- www.zh-wedm.com
扫一扫访问手机商铺
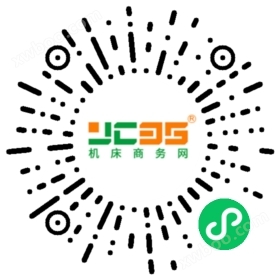
微信扫码进入微名片
-
快走丝线切割机床加工铝件容易短路原因浅析电火花线切割机床在切割铝件时,电腐蚀产生的氧化铝附着钼丝和切割通道的表面,随着氧化层逐渐增厚,导致放电通道的绝缘性增强,电腐蚀性能下降,采样电路不能真实的反馈放电通道的真实情况,控制系统不能给机床进给下达正确指令,进给速度未能正确调整,导致短路。
-
电火花线切割机床加工铝件损耗导电块原因浅析在切割铝件的时候,导电块的会有沟槽的现象,附着在钼丝表面的氧化铝磨损是原因之一。在新钼丝切割铝件的时候,钼丝在导电块上滑动,导电性很好。当钼丝上的氧化铝逐渐附着越来越多,表面形成的氧化铝包裹层使钼丝导电性急剧下降,使得加工正负极发生移动,钼丝变成正极,导电块为负极,二者之间又有一层氧化铝介质,加工一段时间后就会看到钼丝和导电块之间产生小的火花放电。这种放电使导电块被电腐蚀出沟槽,从而影响线切割机床的加工精度等原因产生,以至于设备的正常使用情况。
-
数控电火花线切割机床铝件切割效率低原因浅析铝的熔点比钢,铜,硬质合金都低,导电性比铜低,比钢,硬质合金高。从理论分析利用线切割加工铝件的效率应该比钢件效率高。经过现场实际试验切割,用新钼丝或切割过钢件的钼丝加工铝件,刚开始的时候,加工效率是钢件的2到3倍。但过一段时间后,氧化铝逐渐附着钼丝上,由于氧化铝不导电,使钼丝和铝件之间的导电率降低,不易形成放电通道,切割效率逐渐降低。
-
电火花成型机床/火花机实操之电流参数选择解读电火花成型机床及火花机在加工使用过程中,电流参数的选择对加工的质量有着决定性。电流参数一般有0-9等10个选择:参数为0时,电火花成型机及火花机使用者必须将放电条件顺序的输入(简称为手动);参数为为1-9时,每当改变电流,其它的加工条件会由晶体的记忆体取出并且呈现于加工条件的设定中。参数1-8的规则是参数越小电极消耗越大,反之电极消耗越小。至于火花机加工速度方面则在参数3-4时zui快。而参数越小,则工件表面细腻均匀。面积越小,锐角的电极,则可采用较大
-
中走丝线切割机床过滤水箱的清洗及安装简述中走丝线切割机床循环过滤水箱采用循环式多层过滤方式,长期使用后,水箱中的过滤网和过滤纸芯中积累大量电蚀产物和杂物,影响过滤效果,需将其取出清洗:1将金属软管与箱体之间的链接螺帽拧开,取消顶盖,然后将固定纸芯的螺帽打开,将纸芯取出,用自来水冲洗干净2将金属软管与箱体之间的链接螺帽松开将污水倒尽,把圆形箱体内的污水倒尽,并冲洗干净,再将水箱内的污水排尽,水箱前后有一出水口,将螺帽松开即可3水箱清洗完后,就可以配对乳化液了,配对好以后,将圆形箱放入水箱中,将金属
-
电火花穿孔机脉冲电源使用简述小孔机,电火花穿孔机,电火花打孔机的脉冲间隔的选择选择原则说明:加工工件高度较高时,适当加大脉冲间隔,以利排屑,减少切割处的电蚀污物的生成,使加工较稳定,防止断丝。因为在脉宽档位确定的情况下,间隔在“间隔微调”旋钮确定下,间隔宽度是一定的,所以要调节间隔大小就是旋转“间隔微调”旋钮。在有稳定高频电流指示的情况下,旋转“间隔微调”旋钮时,电流变小表示间隔变大,电流变大表示间隔变小。脉宽的选择选择原则说明:脉冲宽度宽时,放电时间长,单个脉冲的能量大,加工稳定,切割效率高,
-
为什么钼丝安装太松会造成中走丝线切割机床的加工断丝如果钼丝安装太松,则钼丝抖动厉害,不仅会造成断丝,而且由于钼丝的抖动直接影响工件表面粗糙度。但钼丝也不能安装得太紧,太紧内应力增大,也会造成断丝,因此钼丝在切割过程中,其松紧程度要适当,新安装的钼丝,要先紧丝再加工,紧丝时用力不要太大。钼丝在加工一段时间后,由于自身的拉伸而变松。当伸长量较大时,会加剧钼丝振动或出现钼丝在贮丝筒上重叠。使走丝不稳而引起断丝。应经常检查钼丝的松紧程度,如果存在松弛现象,要及时拉紧。钼丝安装。钼丝要按规定的走向绕在贮丝
-
电子尺在电火花穿孔机上的安装应用一般而言,在电火花穿孔机的工作台上安装电子尺,表头放至固定在机床上并且于主尺的下方,安装方式需要根据高速电火花穿孔机加工液溅落方向做调整。还需要注意表头要放置于安装在穿孔机稳定性强的位置,保证输出导线固定位置,数显部位会选择相对设备运动的位置。1、穿孔机安装电子尺放置加工设备上,需要将光学尺放置光滑位置,光学尺、表头放置于机床相对运动的两个不同位置,用百分表测量工作台的主尺安装面与导轨运动是否达到平衡。将百分表固定在机床上,移动工作台使达到平行度为小于0.1mm/